UNIVERSITY OF CALIFORNIA COOPERATIVE EXTENSION
2005
SAMPLE COSTS TO PRODUCE
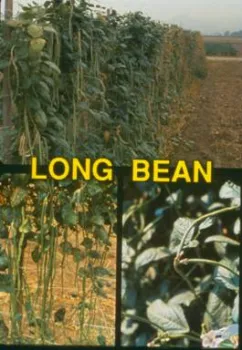
CHINESE LONG BEAN
SAN JOAQUIN VALLEY - SOUTH
Small Farm
Prepared by:
Richard H. Molinar, UC Cooperative Extension Farm Advisor, Fresno County
Michael Yang, UC Agricultural Assistant, Fresno County
Karen M. Klonsky, UC Cooperative Extension Specialist, Department of Agricultural and Resource Economics, UC Davis
Richard L. De Moura, Staff Research Associate, Department of Agricultural and Resource Economics, UC Davis
UNIVERSITY OF CALIFORNIA COOPERATIVE EXTENSION
SAMPLE COSTS TO PRODUCE
CHINESE LONG BEAN
San Joaquin Valley - 2005
STUDY CONTENTS
INTRODUCTION….............................................. 2
ASSUMPTIONS. ........................................ 3
Production Operating Costs.......................... 3
Cash Overhead ...................... 5
Non-Cash Overhead ........................................... 6
REFERENCES ............................................. 8
Table 1. COSTS PER ACRE to PRODUCE CHINESE LONG BEAN .................................. 9
Table 2. COSTS AND RETURNS PER ACRE to PRODUCE CHINESE LONG BEAN ..................................... 10
Table 3. MONTHLY CASH COSTS PER ACRE to PRODUCE CHINESE LONG BEAN ................................. 11
Table 4. RANGING ANALYSIS............................................ 12
Table 5. WHOLE FARM ANNUAL EQUIPMENT, INVESTMENT and OVERHEAD COSTS.......................... 13
Table 6. HOURLY EQUIPMENT COSTS .............................. 13
Table 7. OPERATIONS WITH EQUIPMENT........................... 14
INTRODUCTION
Sample costs to produce Chinese long bean in the San Joaquin Valley are shown in this study. The study is intended as a guide only, and can be used to make production decisions, determine potential returns, prepare budgets and evaluate production loans. The practices described are based on production operations considered typical for this crop and region, but will not apply to every farm. Sample costs for labor, materials, equipment and custom services are based on current figures. "Your Costs" columns in Tables 1 and 2 are provided for entering your farm costs.
The hypothetical farm operations, production practices, overhead, and calculations are described under the assumptions. For additional information or an explanation of the calculations used in the study call the Department of Agricultural and Resource Economics, University of California, Davis, California, (530) 752-3589 or the local UC Cooperative Extension office.
Sample Cost of Production Studies for many commodities can be downloaded at http://coststudies.ucdavis.edu, requested through the Department of Agricultural and Resource Economics, UC Davis, (530) 752-4424 or obtained from the local county UC Cooperative Extension offices. Some archived studies are also available on the website.
The University of California does not discriminate in any of its policies, procedures or practices. The university is an affirmative action/equal opportunity employer.
University of California and USDA, Risk Management Cooperating.
ASSUMPTIONS
The assumptions refer to Tables 1 to 7 and pertain to sample costs to produce Chinese long bean in the San Joaquin Valley. The cultural practices described represent production operations and materials considered typical for a small farm in the region. Costs, materials, and practices in this study will not apply to all farms. Timing of and types of cultural practices will vary among growers within the region and from season to season due to variables such as weather, soil, and insect and disease pressure. The study is intended as a guide only. The use of trade names and cultural practices in this report does not constitute an endorsement or recommendation by the University of California nor is any criticism implied by omission of other similar products or cultural practices.
Farm. This report is based on a hypothetical 10 contiguous acre farm. The land is rented and planted to Asian vegetables. Two acres are planted to Chinese long bean and the remaining acres to other Asian vegetables. The grower and family do the majority of the labor for the operations, but a labor cost (opportunity cost) is shown for each operation.
Production Operating Costs
Land Preparation. A custom operator plows the land one time, discs two times and lists the beds in January/February. After listing, the bed peaks are flattened using a nine-foot pipe (3 rows) towed behind the grower’s tractor. Black plastic (mulch) is then laid by hand (4 hrs per acre x 2 persons) on alternate beds.
Plant. The Chinese long bean seed in alternate years is either purchased new or saved from the previous crop. Therefore, one-half of the new seed cost is charged to the crop each year. The seed is planted in the greenhouse during January. The plant trays hold 50 plants per tray and take about 20 minutes per tray to plant. The germinated plants are transplanted in the field in February. The grower transplants 3,630 plants per acre at a two-foot in-row spacing on 36-inch alternate beds. Holes for the plants are burned or punched in the plastic as the planter plants. Rows are usually 250 to 300 feet long. Two people (16 man hours) can plant one-third acre per day. A second planting can be made in June and is direct seeded using the grower’s tractor and planter, but is not taken into account in this study.
Irrigation. Irrigation includes the water cost and irrigation labor. Lay flat vinyl pipe is laid at the end of the rows and the water is run down the furrows. Irrigation begins in March two to three days after planting. The field is irrigated every five to seven days during March and April, every two to three days during May, June and July. Water at $2.50 per irrigation is assumed to be a typical cost. Water costs were provided from the growers pumping charges for the summer months. Data on total water use in acre-inches was not available. Water costs will vary by pumping setup and irrigation district. A typical water cost in the area is $4.83 per acre-inch. Irrigation labor is calculated as one-half hour per acre per irrigation.
Fertilization. The field is fertilized at planting with soluble 20-20-20 fertilizer dissolved in water at three ounces of liquid fertilizer per plant or one 25-pound bag per two to three acres. (10 pounds per acre in this study). The fertilizer is placed in the planting hole at planting. Labor costs for applying the fertilizer are included in the planting labor.
Crop Protection. The grower builds tunnels over the new transplants for frost protection and warming. Wire hoops (reusable) are spaced down the row every six-feet. Three-foot wide plastic is laid over each side of the hoop and attached to each other at the top with a clothespin. They are opened as needed to allow the plants to grow through and to vent on warm days to prevent burning. It takes one person per day (8 hrs) per acre to set out the hoops and two persons per day per acre to stretch the plastic over the hoops. The tunnels are removed in late-April and takes two-hours per acre with two persons. If the grower plants later, mid-March and after, these costs can be avoided. For the later plantings, the crop protection costs (about $1,200) should be subtracted from the cultural practices in this study.
Trellis System. Six-foot stakes (reusable) are pounded in the ground at six-foot spacing; netting is attached to the stakes to form a trellis that the plants will grow up. It takes two persons one day (8 hours) per acre to pound the stakes and an equal amount of time to install the net. The trellis is removed at the end-of-the season. See Field Cleanup below.
Pest Management. The pesticides, rates, and application practices mentioned in this cost study are listed in the UC IPM Pest Management Guidelines – Beans. Pesticides mentioned in this study are not recommendations, but those commonly used in the region. For information and pesticide use permits, contact the local county Agricultural Commissioner’s office. For information on other pesticides available, pest identification, monitoring, and management, visit the UC IPM website at www.ipm.ucdavis.edu. Pest control costs can vary considerably each year depending upon local conditions and pest populations in any given year. Adjuvants are recommended for many pesticides for effective control and are an added cost. The adjuvants in this study are not included as a cost in the applications.
Weeds. The furrows are hand sprayed using a backpack sprayer with Roundup in April or May and in July. Black plastic provides weed control on the beds. The field is hand weeded in June and takes three-hours per acre. Additional weeding may be required.
Insects. Lannate is applied in May for lygus and aphid control. The grower applies the spray using a backpack sprayer. Growers with a second planting in June will most likely apply a similar spray to that planting in August. Also, spider mites can be a problem in the June planting and a spray with oil or soap provides some control.
Diseases. Possible diseases are mosaic virus, which is spread by aphids. Virus control is done by controlling aphid populations and using virus free or certified seed.
Pickup/ATV. Costs for a 1/2-ton pickup are included in the study. The pickup and a trailer are used for hauling the harvested beans to the packing shed and is included in that cost. The pickup and trailer are used to haul the removed tunnels, mulch and netting to the landfill and the costs are included in the respective operations. In addition, the grower drives another 250 miles per acre for farming purposes or to sell his crop at a farmers market.
Field Cleanup. In August or after the last harvest, the plants are chopped by hand, and the stakes, netting, and mulch are removed. One person can chop the plants and remove the mulch at the rate of three 250-foot rows per eight-hour day (approximately 80 hours per acre).
Harvest. The February planting is harvested May through July (12 weeks). The beans are picked by hand every 2 to 3 days, packed in 30-pound boxes and hauled to a packinghouse. The crop is harvested May through November for growers with double plantings. The packing shed quits taking long beans at the end of October, so any produced after that are sold at farmers or the local markets. Based on picking information on other vegetable crops, it is assumed that a person can pick 1.33 thirty-pound boxes per hour. The grower delivers the product to the packinghouse, local or farmers market. It is assumed one load of 19 boxes is delivered at the end of each picking day.
Yields. The crop yields an average of 440 thirty-pound boxes or 13,200 pounds per acre per planting. Yields are based on grower input.
Returns. The weighted average (fresh & wholesale) returns used in this study are approximated at $0.75 per pound ($22.50/box) and used to calculate returns over a range of yields. It is assumed that 70% of the beans are sold wholesale and 30% through farmers or local markets. We assumed the growers would receive an average of $1.00 per pound at the farmers on local markets. The USDA Wholesale Market reports for California July through September product averaged $0.93 per pound. Assuming that 70% of the wholesale price is the net return to the grower, the grower would receive $0.65 per pound.
Labor. Labor rates of $12.42 per hour for machine operators and $9.32 for general labor includes payroll overhead of 38%. The basic hourly wages are $9.00 for machine operators and $6.75 for general labor. The overhead includes the employers’ share of federal and California state payroll taxes, workers' compensation insurance for truck crops (code 0172), and a percentage for other possible benefits. Workers’ compensation costs will vary among growers, but for this study the cost is based upon the average industry final rate as of January 1, 2005 (California Department of Insurance). Labor for operations involving machinery are 20% higher than the operation time given in Table 1 to account for the extra labor involved in equipment set up, moving, maintenance, work breaks, and field repair.
Equipment Operating Costs. Repair costs are based on purchase price, annual hours of use, total hours of life, and repair coefficients formulated by American Society of Agricultural Engineers (ASAE). Fuel and lubrication costs are also determined by ASAE equations based on maximum Power Take Off (PTO) horsepower, and fuel type. Prices for on-farm delivery of diesel and gasoline are $1.51 and $2.05 per gallon, respectively. The cost includes a 2% local sales tax on diesel fuel and 8% sales tax on gasoline. Gasoline also includes federal and state excise tax, which are refundable for on-farm use when filing your income tax. The fuel, lube, and repair cost per acre for each operation in Table 1 is determined by multiplying the total hourly operating cost in Table 6 for each piece of equipment used for the selected operation by the hours per acre. Tractor time is 10% higher than implement time for a given operation to account for setup, travel and down time.
Interest On Operating Capital.Interest on operating capital is based on cash operating costs and is calculated monthly until harvest at a nominal rate of 7.65% per year. A nominal interest rate is the typical market cost of borrowed funds. The interest cost of post harvest operations is discounted back to the last harvest month using a negative interest charge.
Risk. Production risks should not be minimized. While this study makes every effort to model a production system based on typical, real world practices, it cannot fully represent financial, agronomic and market risks, which affect the profitability and economic viability.
Cash Overhead
Cash overhead consists of various cash expenses paid out during the year that are assigned to the whole farm and not to a particular operation. These costs include property taxes, interest on operating capital, office expenses, liability and property insurance, and investment repairs.
Property Taxes. Counties charge a base property tax rate of 1% on the assessed value of the property. In some counties special assessment districts exist and charge additional taxes on property including equipment, buildings, and improvements. For this study, county taxes are calculated as 1% of the average value of the property. Average value equals new cost plus salvage value divided by 2 on a per acre basis.
Insurance. Insurance for farm investments varies depending on the assets included and the amount of coverage. Property insurance provides coverage for property loss and is charged at 0.69% of the average value of the assets over their useful life. Liability insurance covers accidents on the farm and costs $429 for the entire farm.
Office Expense. Office and business expenses are estimated at $10 per acre. These expenses include office supplies, telephones, bookkeeping, accounting, and legal fees. The cost is a general estimate and not based on any actual data.
Land Rent. The 10 acres are rented for cash at $300 per acre. The rented land includes the irrigation system that is maintained by the landlord. The landowner also pays the property tax on the rented land. Land rents range from $250 to $350 per acre.
Investment Repairs. Annual maintenance except for the greenhouse (20%) is calculated as two percent of the purchase price.
Non-cash Overhead
Non-cash overhead is calculated as the capital recovery cost for equipment and other farm investments.
Capital Recovery Costs. Capital recovery cost is the annual depreciation and interest costs for a capital investment. It is the amount of money required each year to recover the difference between the purchase price and salvage value (unrecovered capital). It is equivalent to the annual payment on a loan for the investment with the down payment equal to the discounted salvage value. This is a more complex method of calculating ownership costs than straight-line depreciation and opportunity costs, but more accurately represents the annual costs of ownership because it takes the time value of money into account (Boehlje and Eidman). The formula for the calculation of the annual capital recovery costs is ((Purchase Price – Salvage Value) x Capital Recovery Factor) + (Salvage Value x Interest Rate).
Salvage Value. Salvage value is an estimate of the remaining value of an investment at the end of its useful life. For farm machinery (tractors and implements) the remaining value is a percentage of the new cost of the investment (Boehlje and Eidman). The percent remaining value is calculated from equations developed by the American Society of Agricultural Engineers (ASAE) based on equipment type and years of life. The life in years is estimated by dividing the wear out life, as given by ASAE by the annual hours of use in this operation. For other investments including irrigation systems, buildings, and miscellaneous equipment, the value at the end of its useful life is zero. The salvage value for land is the purchase price because land does not depreciate. The purchase price and salvage value for equipment and investments are shown in the tables.
Capital Recovery Factor. Capital recovery factor is the amortization factor or annual payment whose present value at compound interest is 1. The amortization factor is a table value that corresponds to the interest rate used and the life of the machine.
Interest Rate. The interest rate of 6.01% used to calculate capital recovery cost is the USDA-ERS’s ten-year average of California’s agricultural sector long-run rate of return to production assets from current income. It is used to reflect the long-term realized rate of return to these specialized resources used effectively in the agricultural sector.
Tools. This includes shop tools, hand tools, and miscellaneous field tools. The tools are an estimated value and not taken from any specific data.
Irrigation. The grower owns 1,732 feet of vinyl flat pipe to deliver the water to the furrows. The pipe was purchased for the farm and the cost is allocated among the various crops.
Greenhouse. The grower builds a greenhouse of PVC pipe and plastic to start the plants and for some plant storage. The greenhouse is 20 feet x 20 feet. The plastic cover may need to be replaced in one or two years. The greenhouse is assumed to be used for other crops on the farm and the cost is allocated accordingly.
Equipment. Farm equipment is purchased new or used, but the study shows the current purchase price for new equipment. The new purchase price is adjusted to 60% to indicate a mix of new and used equipment. Annual ownership costs for equipment and other investments are shown in the Whole Farm Annual Equipment, Investment, and Business Overhead Costs table. Equipment costs are composed of three parts: non-cash overhead, cash overhead, and operating costs. Both of the overhead factors have been discussed in previous sections. The operating costs consist of repairs, fuel, and lubrication and are discussed under operating costs.
Table Values. Due to rounding, the totals may be slightly different from the sum of the components.
REFERENCES
American Society of Agricultural Engineers. 1994. American Society of Agricultural Engineers Standards Yearbook. Russell H. Hahn and Evelyn E. Rosentreter (ed.) St. Joseph, Missouri. 41st edition.
Barker, Doug. 2005. California Workers’ Compensation Rating Data for Selected Agricultural Classifications as of January 1, 2005. California Department of Insurance, Rate Regulation Branch.
Boelje, Michael D., and Vernon R. Eidman. 1984. Farm Management. John Wiley and Sons. New York, New York
California State Automobile Association. 2004. Gas Price Survey 2004. AAA Public Affairs, San Francisco,
California State Board of Equalization. Fuel Tax Division Tax Rates. Internet accessed January 2005. http://www.boe.ca.gov/sptaxprog/spftdrates.htm.
Energy Information Administration. 2004. Weekly Retail on Highway Diesel Prices. Internet accessed January 2005. http://tonto.eis.doe.gov/oog/info/wohdp.
United States Department of Agriculture-Economic Reporting Service. Farm Financial Ratios Indicating Solvency and Profitability 1960 – 02, California. 2002. Internet; accessed January 4, 2005. www.ers.usda.gov/data/farmbalancesheet/fbsdmu.htm
Unknown. Yard Long Beans. http://www.webindia123.com/garden/vegie/longbeans.htm. Internet accessed November 18, 2004.
Van Horn, Mark, and Claudia Myers. Chinese Long Bean, Yard-long Bean, Asparagus Bean. Student Experimental Farm, UC Davis. http://www.island.wsu.edu/crops/chinesel.htm. Internet accessed November 18, 2004.
For information concerning University of California publications contact UC DANR Communications Services (1-800-994-8849), online at http://anrcatalog.ucdavis.edu or your local county Cooperative Extension office.
Cash and Labor Costs per Acre | ||||||||
---|---|---|---|---|---|---|---|---|
Operation | Operation Time (Hrs/A) | Field Labor (Hrs/A) | Labor Cost | Fuel, Lube & Repairs | Material Cost | Custom/Rent | Total Cost | Your Cost |
Cultural: | ||||||||
Plant: Greenhouse (seed) | 0.00 | 24.00 | 224 | 0 | 80 | 0 | 304 | |
Land Prep: Plow, Disc, List | 0.00 | 0.00 | 0 | 0 | 0 | 100 | 100 | |
Land Prep: Flatten Bed Tops | 0.33 | 0.00 | 5 | 1 | 0 | 0 | 6 | |
Land Prep: Lay Black Plastic on Alternate Rows | 0.00 | 8.00 | 75 | 0 | 116 | 0 | 191 | |
Plant: Transplants from greenhouse. | 0.00 | 48.00 | 447 | 0 | 6 | 0 | 453 | |
Crop Protection: Install Tunnels | 0.00 | 24.00 | 224 | 0 | 457 | 0 | 681 | |
Irrigate: (water & labor) | 0.00 | 19.00 | 177 | 0 | 95 | 0 | 272 | |
Trellis: Install | 0.00 | 32.00 | 298 | 0 | 1,326 | 0 | 1,624 | |
Crop Protection: Remove Tunnels | 0.50 | 4.00 | 45 | 6 | 0 | 5 | 56 | |
Weed: Hand Spray Furrow (Roundup) | 0.00 | 3.00 | 28 | 0 | 16 | 0 | 44 | |
Weed: Hand Hoe | 0.00 | 3.00 | 28 | 0 | 0 | 0 | 28 | |
Field Cleanup: Chop Plants, Trellis, Mulch | 0.50 | 80.00 | 753 | 6 | 0 | 7 | 766 | |
Miscellaneous Pickup Use | 5.00 | 0.00 | 75 | 59 | 0 | 0 | 134 | |
TOTAL CULTURAL COSTS | 6.33 | 245.00 | 2,378 | 73 | 2,096 | 111 | 4,658 | |
Harvest: | ||||||||
Hand Pick | 0.00 | 330.82 | 3,083 | 0 | 440 | 0 | 3,523 | |
Haul | 23.15 | 0.00 | 345 | 291 | 0 | 0 | 636 | |
TOTAL HARVEST COSTS | 23.15 | 330.82 | 3,428 | 291 | 440 | 0 | 4,159 | |
Interest on operating capital | 179 | |||||||
TOTAL OPERATING COSTS/ACRE | 5,806 | 364 | 2,536 | 111 | 8,996 | |||
CASH OVERHEAD: | ||||||||
Liability Insurance | 43 | |||||||
Office Expense | 10 | |||||||
Land Rent | 300 | |||||||
Property Taxes | 11 | |||||||
Property Insurance | 8 | |||||||
Investment Repairs | 10 | |||||||
TOTAL CASH OVERHEAD COSTS | 381 | |||||||
TOTAL CASH COSTS/ACRE | 9,377 | |||||||
Non-Cash Overhead (Capital Recovery) | Per Producing | Annual Cost | ||||||
Acre | Capital Recovery | |||||||
Plastic Greenhouse 20x20' | 35 | 8 | 8 | |||||
Flat Irrigation Pipe | 46 | 25 | 25 | |||||
Miscellaneous Field Tools | 100 | 24 | 24 | |||||
Equipment | 1,554 | 222 | 222 | |||||
TOTAL NON-CASH OVERHEAD COSTS | 1,735 | 279 | 279 | |||||
TOTAL COSTS/ACRE | 9,656 |
Quantity/Acre | Unit | Price or Cost/Unit | Value or Cost/Acre | Your Cost | |
---|---|---|---|---|---|
GROSS RETURNS | |||||
Long Bean | 13,200.00 | lb | 0.75 | 9,900 | |
OPERATING COSTS | |||||
Carton: | |||||
Trays - Planting 50 Cell | 73.00 | each | 1.00 | 73 | |
Boxes 30 lb | 440.00 | each | 1.00 | 440 | |
Seed: | |||||
Seed - Chinese Long Bean (1/2 cost) | 0.50 | lb | 14.50 | 7 | |
Custom: | |||||
Land Preparation | 1.00 | acre | 100.00 | 100 | |
Landfill Fee | 555.00 | lb | 0.02 | 11 | |
Crop Protect: | |||||
Plastic Black 3 ft x 2000 ft/roll. 1mil | 7,250.00 | foot | 0.02 | 116 | |
Plastic Clear 3 ft x 2000 ft/roll | 14,500.00 | foot | 0.02 | 217 | |
Wire Hoops (reusable) | 1,200.00 | each | 0.20 | 240 | |
Stakes - 5 ft (reusable) | 1,200.00 | each | 0.99 | 1,188 | |
Netting for Trellis 320 ft/roll | 7,250.00 | foot | 0.02 | 138 | |
Fertilizer: | |||||
20-20-20 | 10.00 | lb | 0.57 | 6 | |
Irrigation: | |||||
Water | 38.00 | each | 2.50 | 95 | |
Herbicide: | |||||
Roundup Ultra Max | 32.00 | fl oz | 0.49 | 16 | |
Labor (machine) | 35.38 | hrs | 12.42 | 439 | |
Labor (non-machine) | 575.82 | hrs | 9.32 | 5,367 | |
Fuel - Gas | 121.43 | gal | 2.05 | 249 | |
Fuel - Diesel | 0.63 | gal | 1.51 | 1 | |
Lube | 37 | ||||
Machinery repair | 77 | ||||
Interest on operating capital @ 7.65% | 179 | ||||
TOTAL OPERATING COSTS/ACRE | 8,996 | ||||
NET RETURNS ABOVE OPERATING COSTS | 904 | ||||
CASH OVERHEAD COSTS: | |||||
Liability Insurance | 43 | ||||
Office Expense | 10 | ||||
Land Rent | 300 | ||||
Property Taxes | 11 | ||||
Property Insurance | 8 | ||||
Investment Repairs | 10 | ||||
TOTAL CASH OVERHEAD COSTS/ACRE | 381 | ||||
TOTAL CASH COSTS/ACRE | 9,377 | ||||
NON-CASH OVERHEAD COSTS (Capital Recovery) | |||||
Plastic Greenhouse 20x20' | 8 | ||||
Flat Irrigation Pipe | 25 | ||||
Miscellaneous Field Tools | 24 | ||||
Equipment | 222 | ||||
TOTAL NON-CASH OVERHEAD COSTS/ACRE | 279 | ||||
TOTAL COSTS/ACRE | 9,656 | ||||
NET RETURNS ABOVE TOTAL COSTS | 244 |
Beginning JAN 05 Ending DEC 05 | JAN 05 | FEB 05 | MAR 05 | APR 05 | MAY 05 | JUN 05 | JUL 05 | AUG 05 | SEP 05 | OCT 05 | NOV 05 | DEC 05 | TOTAL |
---|---|---|---|---|---|---|---|---|---|---|---|---|---|
Cultural: | |||||||||||||
Plant: Greenhouse | 304 | 304 | |||||||||||
Land Prep: Plow, Disc, List | 100 | 100 | |||||||||||
Land Prep: Flatten Bed Tops | 6 | 6 | |||||||||||
Land Prep: Black Plastic on Alternate Rows | 191 | 191 | |||||||||||
Plant: Transplants. Fertilize: (20-20-20) | 453 | 453 | |||||||||||
Crop Protection: Install Tunnels | 681 | 681 | |||||||||||
Irrigate: (water & labor) | 29 | 29 | 72 | 72 | 72 | 272 | |||||||
Trellis: Install | 1,624 | 1,624 | |||||||||||
Crop Protection: Remove Tunnels | 56 | 56 | |||||||||||
Weed: Hand Spray Furrow (Roundup) | 22 | 22 | 44 | ||||||||||
Weed: Hand Hoe | 28 | 28 | |||||||||||
Field Cleanup: Chop Plants, Trellis, Mulch | 766 | 766 | |||||||||||
Miscellaneous Pickup Use | 17 | 17 | 17 | 17 | 17 | 17 | 17 | 17 | 134 | ||||
TOTAL CULTURAL COSTS | 421 | 1,348 | 1,669 | 123 | 116 | 110 | 88 | 783 | 0 | 0 | 0 | 0 | 4,658 |
Harvest: | |||||||||||||
Harvest: Hand Pick | 1,162 | 1,198 | 1,162 | 3,523 | |||||||||
Haul | 210 | 216 | 210 | 636 | |||||||||
TOTAL HARVEST COSTS | 0 | 0 | 0 | 0 | 1,372 | 1,414 | 1,372 | 0 | 0 | 0 | 0 | 0 | 4,159 |
Interest on operating capital @ 7.65% | 3 | 11 | 22 | 23 | 32 | 42 | 51 | -5 | 179 | ||||
TOTAL OPERATING COSTS/ACRE | 423 | 1,359 | 1,691 | 145 | 1,521 | 1,566 | 1,512 | 778 | 0 | 0 | 0 | 0 | 8,996 |
OVERHEAD: | |||||||||||||
Liability Insurance | 43 | 43 | |||||||||||
Office Expense | 1 | 1 | 1 | 1 | 1 | 1 | 1 | 1 | 10 | ||||
Land Rent | 300 | 300 | |||||||||||
Property Taxes | 11 | 11 | |||||||||||
Property Insurance | 8 | 8 | |||||||||||
Investment Repairs | 1 | 1 | 1 | 1 | 1 | 1 | 1 | 1 | 1 | 1 | 1 | 1 | 10 |
TOTAL CASH OVERHEAD COSTS | 21 | 2 | 45 | 2 | 2 | 2 | 2 | 302 | 1 | 1 | 1 | 1 | 381 |
TOTAL CASH COSTS/ACRE | 444 | 1,361 | 1,736 | 148 | 1,523 | 1,569 | 1,514 | 1,080 | 1 | 1 | 1 | 1 | 9,377 |
COSTS PER ACRE AT VARYING YIELD TO PRODUCE CHINESE LONG BEAN | |||||||
---|---|---|---|---|---|---|---|
Boxes/Acre: | 250 | 290 | 340 | 390 | 440 | 490 | 540 |
YIELD (lbs/acre) | |||||||
7,500 | 8,700 | 10,200 | 11,700 | 13,200 | 14,700 | 16,200 | |
OPERATING COSTS/ACRE: | |||||||
Cultural Cost | 4,658 | 4,658 | 4,658 | 4,658 | 4,658 | 4,658 | 4,658 |
Harvest Cost (Pick & Haul) | 2,363 | 2,741 | 3,214 | 3,686 | 4,159 | 4,632 | 5,104 |